Table Of Content
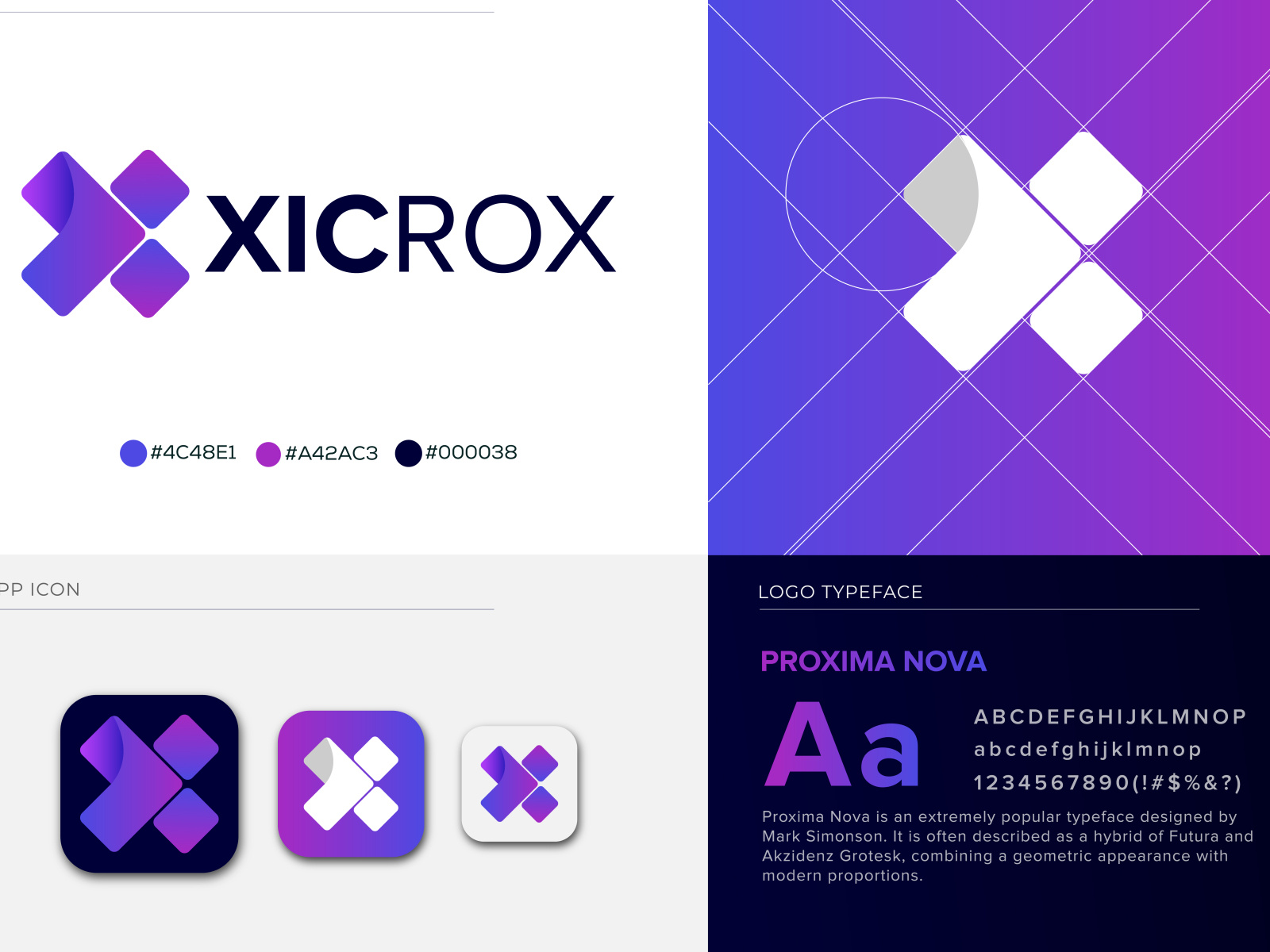
In the absence of the above reasons, the part must be combined with another part or with the product body to reduce the part count in the final assembly. Design for X (DFX) has many such focus areas for design improvement. Some of them such as DFM, DFA, and DFMA are more popular than others. The design for X process comes with certain characteristics that make it a better alternative to its traditional counterparts. Albert Einstein once said, “The best design is the simplest one that works.” But a simple design can be difficult and time-consuming to create.
School of Engineering, University of Abertay, Dundee, UK
DFM concentrates on ensuring that the end product can be manufactured in the most cost-effective, efficient, and environmentally friendly way possible. Whether you are looking to boost efficiencies in your organization or prepping for the PMP certification exam, this primer has provided the core knowledge you need to master this concept. Design for X (DfX) is one of the tools used in the “Manage Quality” process according to the PMBOK Guide 6th Edition. Use the Boston Engineering customer portal to submit service requests, get status updates, and Check PLM/IIoT KPIs.
Design to Cost (DTC)
Careful choices need to be made concerning logistics, materials, and manufacturing methods. DFR is used to produce a product that can perform its functions under predetermined conditions for a certain period. Without careful management, DFR methods can lead to budget overruns, as there is no set standard for the concept of reliability. Interested in providing your product development team with DFX skills? Learn More about our Applied DFX process and development workshops. DfX actively brings in more stakeholders like manufacturing partners earlier for a team-based approach.
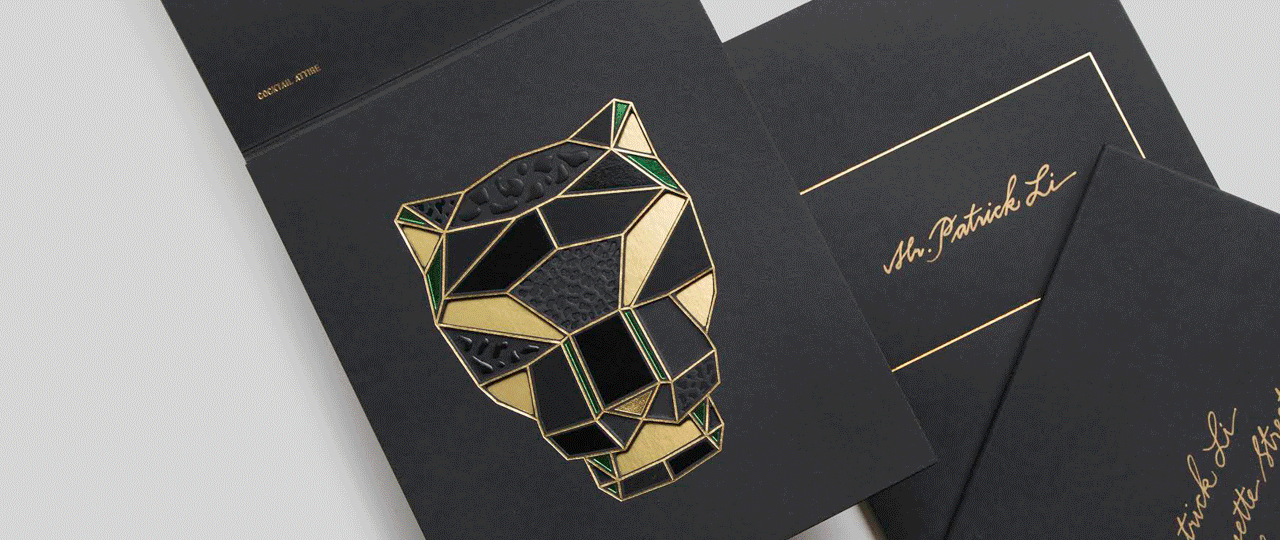
Design for Manufacturing and Assembly
Design for cost and design to cost (DTC) are a set of DFX cost management techniques to control the cost of product development and manufacturing. The design intent is to create a product considering cost as a design parameter in addition to the schedule, scope and features. Design for testing refers to building testing methods into the product during the design stage to make it easy and economical to test the various product attributes and functions. The aim is to detect any crucial defects or issues with minimum intervention in the assembly line or during the packaging phase.
The X in DFX stands for Excellence, but this concept can cover any number of parameters. X can represent any objective that a design team wishes to accomplish. You can, for example, Design for Manufacturability, for Reliability, Quality, Sustainability, or Ease of Assembly. You can even substitute X with a more precise goal, such as Design for Kickstarter.
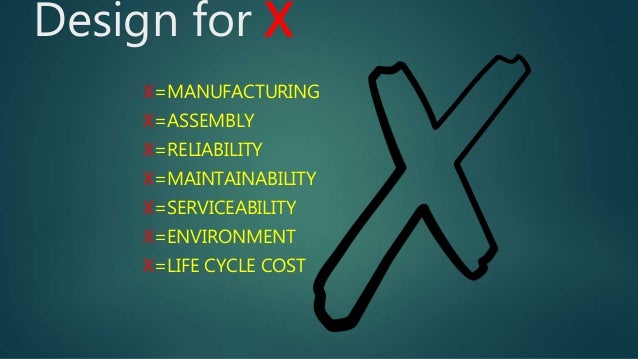
CATIA Mechanical Designer
If X is defined as designing for the circular economy, then stakeholders across all levels will work towards this goal. DFQ seeks to enhance the performance, reliability, durability, serviceability, and aesthetics of a product. Rigorous quality checks are implemented in every stage of the design and manufacturing processes. Understanding of DFX principles within the larger context of product design and development will help you reach your objectives without creating additional issues.
Production-operations phase
Diverse engineering skills drive the future of X-ray science - Argonne National Laboratory
Diverse engineering skills drive the future of X-ray science.
Posted: Wed, 23 Feb 2022 08:00:00 GMT [source]
The traditional engineering process is a linear progression from one step to another. In a traditional process, issues are detected after a design has been made. DFX concentrates on resolving issues during the design stage, not afterward. With DFX methods, simulations are used instead of physical prototype tests.
Apparel design made easy
The target here is to design a system with high supply chain efficiency, less inventory cost, and less or zero waste. Furthermore, you should consider error detection in the design step. This can be challenging when a company has a fixed design cost yet still has to meet customer expectations.
Three Digital Product & Solution Development Considerations
Even small changes to the internal design of an Apple Watch can be huge. By making the logic board thinner, this next-generation Apple Watch could fit additional components inside. Whether this manifests in a bigger battery or other components remains to be seen. Apple is believed to be working on “the biggest overhaul yet” to the Apple Watch’s design.
On the other hand, Design for Excellence is a team-based approach and involves suppliers, cooperation between different parties, and the project management team. An iteration refers to repeating a process until the desired outcome is received. Several iterations are required to produce a satisfactory design, which is costly and time-consuming.
Bloomberg has described the redesign as the “biggest overhaul yet” to the Apple Watch. “I’m all about gardens connecting the architecture into the landscape,” landscape architect Timothy John Palcic tells AD PRO. He used a limited palette of chartreuse and dark hues that nod to the brick exterior and arranged benches to create intimate seating areas within the larger English-garden-inspired space.
For example, at Protolabs, we take your designs from the early quoting and design iterations in our online digital platform, through the prototyping process, and finally to manufactured end-use parts and delivery. Design to cost and design to standards serves cost reduction in production operations, or respectively supply chain operations. Except for luxury goods or brands (e.g., Swarovski crystals, Haute couture fashion, etc.), most goods, even exclusive products, rely on cost reduction, if these are mass produced. The same is valid for the functional production strategy of mass customization. DFX techniques ensure that the main X objective is the focus of every stage of product development and manufacturing process.
Having a good idea about how design for X can do so much more than good old engineering design practices will help us understand why more and more companies are taking the leap to design for X. This is where design for excellence (aka design for X and DFX) comes in. The term “design for X” first made an appearance at the Keys Conference in 1990 and in the AT&T Technological journal. The papers even suggest that the two authors were not aware of each other, showing that the movement towards the same goal had started independently. With tailoring a top fashion trend of late, there have never been more stylish suiting options.
No comments:
Post a Comment